Mängel an elektrischen Anlagen, beispielsweise aufgrund nicht fachgerechter Planung oder Montage, Verschleiß durch Schaltvorgänge oder kurzen Überlastungen, sind Untersuchungen der deutschen Versicherungswirtschaft zufolge eine häufige Ursache für Brände.
Wiederkehrende Prüfungen, beispielsweise mit einer Wärmebildkamera, können Brandrisiken verringern und kostspielige Anlagenstillstände vermeiden. Im laufenden Anlagenbetrieb lassen sich damit thermische Schwachstellen dank des berührungslosen Messprinzips aus sicherer Entfernung in einem Arbeitsschritt lokalisieren und zugleich dokumentieren.
Probleme können einfacher und schneller erkannt, Brand- und Unfallgefahren minimiert, Folgeschäden und Produktionsausfälle vermieden werden. Die Lokalisierung potenzieller Risiken und die Dokumentation von Anlagenzuständen sichern Werte, steigern die Zuverlässigkeit elektrischer Anlagen und schaffen mehr Rechtssicherheit für Anlagenbetreiber.
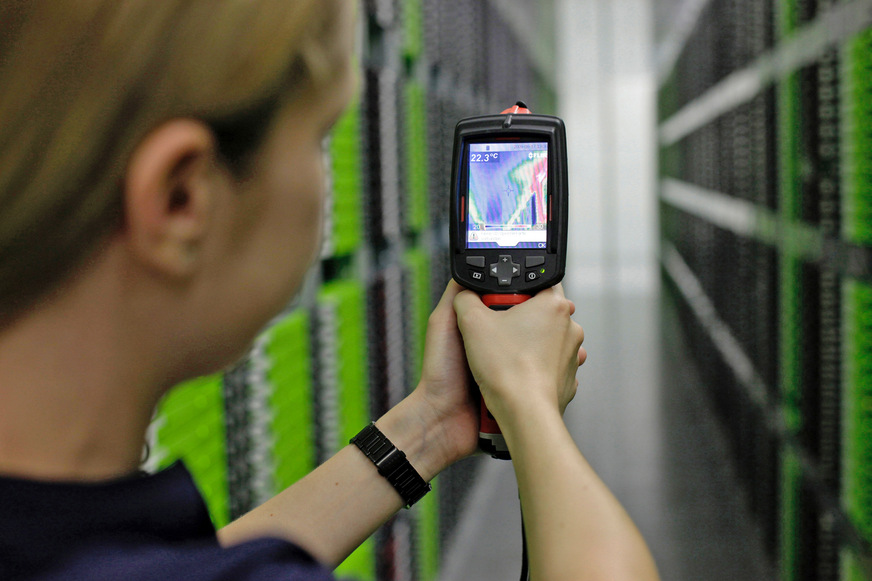
Bild: STRATO AG
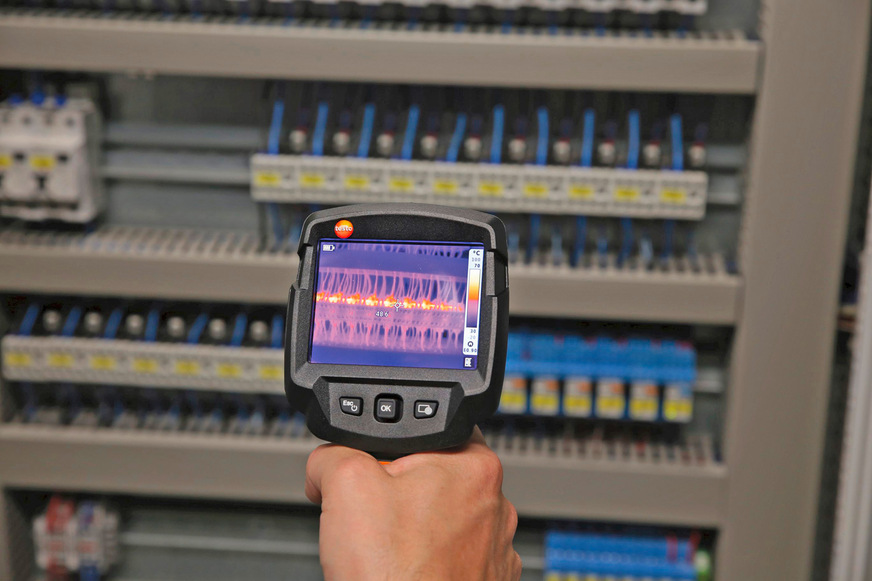
Bild: Testo
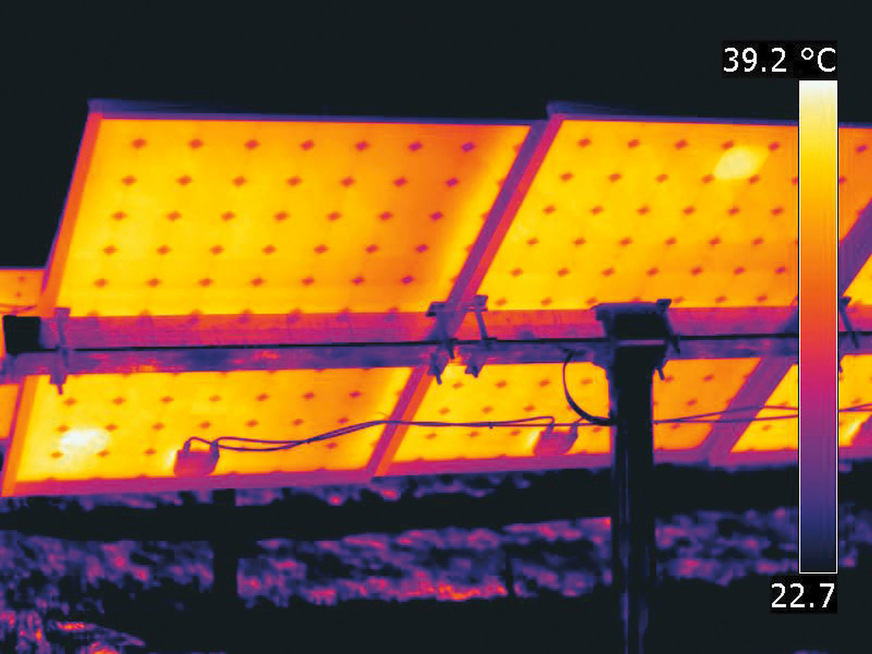
Bild: Flir Systems
Vorteile und Möglichkeiten der Elektrothermografie
Die Elektrothermografie beruht im Wesentlichen auf der ohmschen Verlustleistung Strom durchflossener Leiter und dem Widerstand, den der Stromfluss in der Leitung, an Material- oder Bauteilübergängen erfährt. Dieser bewirkt eine Erwärmung und Temperaturerhöhung, die proportional zum Übergangswiderstand und dem Quadrat der Strombelastung ist. Erhöhte Übergangswiderstände können durch zu geringe Leitungs- und Verbindungsquerschnitte, Korrosion, Alterung und Ermüdung etc. auftreten.
Da Fehler und Probleme als untypische Erwärmungen (sogenannte Hotspots) in Erscheinung treten, eignet sich die Thermografie für alle Anlagen, die Strom durchflossene Leiter enthalten. Deshalb können Nieder-, Mittel- und Hochspannungsanlagen, Mess-, Steuer- und Regeltechnikschränke oder Sicherungskästen mit IR-Kameras ebenso kontrolliert werden, wie Kabeltrassen, Transformatoren, elektrisch betriebene Maschinen oder Photovoltaik(PV)-Anlagen.
Überhitzte Anlagenbauteile können nicht nur Schäden verursachen, Nutzer oder das Bedienpersonal gefährden und Brände auslösen. Auch Leistungseinbußen, die einen wirtschaftlichen Anlagenbetrieb beeinträchtigen können, sind eine mögliche Folge. Bereits geringe Teilausfälle von 10 bis 15 % können zu Mindererträgen führen, die beispielsweise eine PV-Anlage während ihrer Betriebslaufzeit unrentabel machen.
Da Fehler frühzeitig erkannt und behoben werden können, lassen sich auch Betriebsausfallzeiten minimieren. Durch eine kontinuierliche thermografische Überwachung lassen sich Wartungs- und Instandhaltungsintervalle optimieren, was hilft, Betriebskosten zu senken und die Zuverlässigkeit und Wirtschaftlichkeit von Anlagen zu steigern.
Anforderungen an die IR-Kamera
In der professionellen Elektrothermografie spielt die Qualität der Wärmebilder eine wichtige Rolle. Eine zu geringe Detektorauflösung kann nämlich zu Fehlmessungen führen, die fatale Folgen haben können (7). Deshalb sind die Anforderungen an die Auflösung des Infrarotdetektors, die thermische und geometrische Auflösung oder an die Qualität der Objektive in der Elektro-Thermografie besonders hoch.
Für einfache Messaufgaben im Elektro-Handwerk, etwa für die Kontrolle von Kabeltrassen, können zwar eine Detektorauflösung ab 160 × 120 Pixel und eine thermische Auflösung (NETD) ≤ 0,15 K bereits ausreichen.
Für qualifizierte Elektrothermografie-Anwendungen muss eine Wärmebildkamera deutlich höhere Anforderungen erfüllen (siehe auch DIN 54 191 [1], VdS 2859 [7] und VATh-Richtlinie für Elektrothermografie [11]): Der Detektor sollte über eine IR-Auflösung von mindestens 320 × 240 Pixel und einen NETD ≤ 0,08 K verfügen. Die geometrische Auflösung (IFOV) sollte ≤ 2 mrad bei Verwendung eines Normalobjektivs sein.
Noch bessere Wärmebildqualitäten ermöglichen aktuelle High-End-Kameras mit Detektorauflösungen ab 640 × 480 Pixel, einem NETD ≤ 0,05 K und einem IFOV ≤ 1 („Wärmebilder in Fotoqualität“, TGA 11-2018).
Zu den weiteren Anforderungen zählen der Temperatur-Messbereich, der zwischen – 20 bis + 500 °C liegen sollte, das messbare LW-Spektrum sollte 7,5 bis 14 μm und die Bildfrequenz ≥ 20 Hz betragen.
Abhängig von der Messaufgabe sollte wahlweise ein Normal-, Weitwinkel- oder Teleobjektiv verwendet werden können. Empfohlen wird ein externes oder schwenkbares Display, weil es Messungen in beengten räumlichen Verhältnissen erleichtert.
Sowohl der Emissionsgrad (materialspezifischer Wärmeabstrahl-Kennwert) als auch die reflektierte Temperatur und die Umgebungstemperatur sollten individuell einstellbar sein. Zu den Messfunktionen sollten eine Temperatur-Bereichsskala, eine Messpunkt(Spot)-, Isothermen-, Messflächen- und eine automatische Hotspot-Suchfunktion gehören.
Darüber hinaus ist eine jährliche Kalibrierung der Kameratechnik erforderlich (Kosten: ca. 1500 Euro/a je nach Kamera und Objektivanzahl).
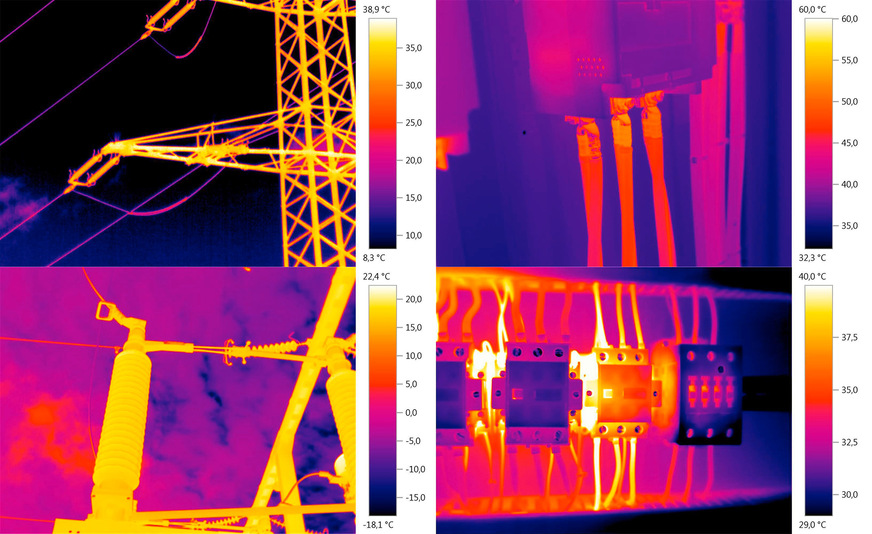
Bild: Testo
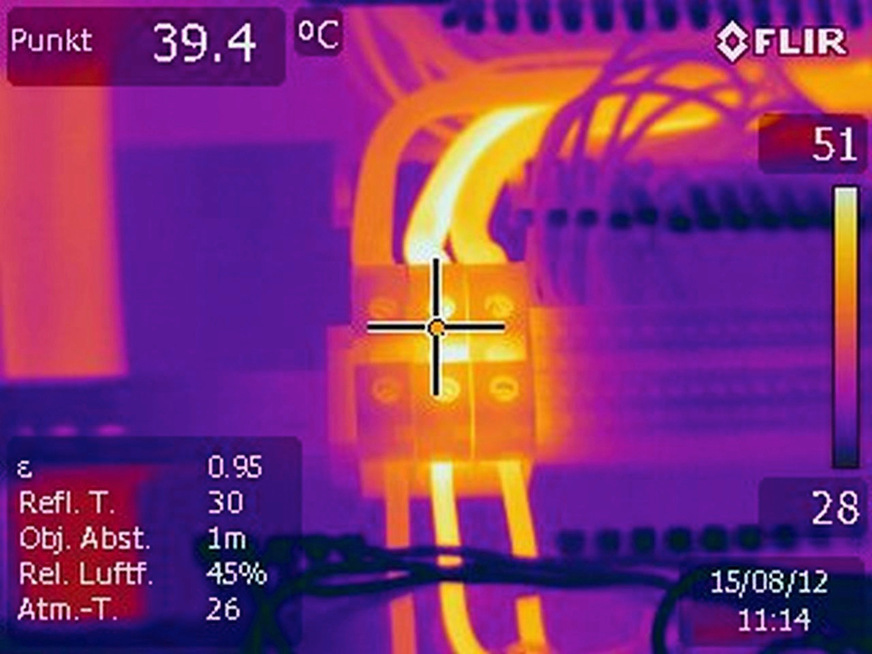
Bild: Flir Systems
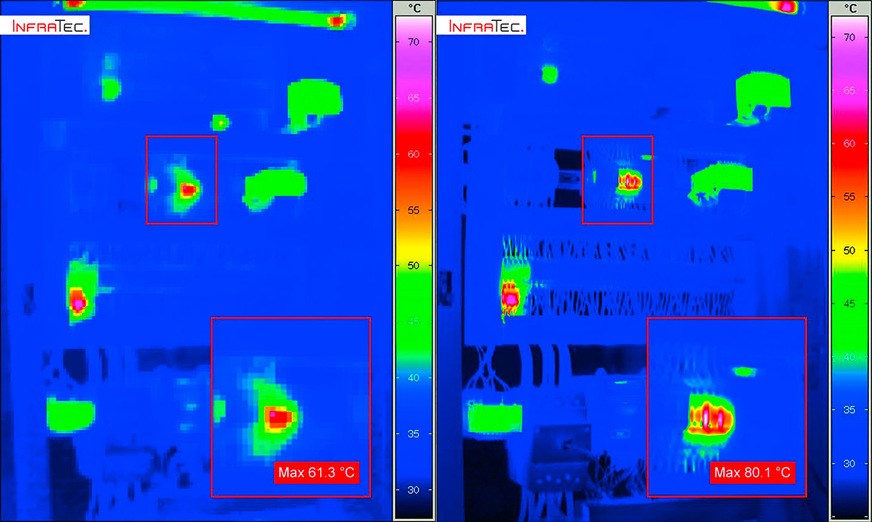
Bild: InfraTec
Anforderungen an den Thermografen
Da Elektroanlagen besonderen Brandrisiken ausgesetzt sind und sich beauftragende Unternehmen auf entsprechende Messungen verlassen müssen, werden an einen qualifizierten Elektrothermografie-Dienstleister besondere Anforderungen gestellt.
Er muss nicht nur die IR-Kamera bedienen, sondern bei der Aufnahme auch mögliche Fehlerquellen und Grenzen der Thermografie kennen und Messergebnisse bei der Auswertung korrekt bewerten können. Das setzt Fachwissen aus den Bereichen Optik, Wärmestrahlung, Wärmeleitung, Messtechnik und Materialkunde voraus. Kenntnisse über die Funktionsweise, den technischen Aufbau oder verwendete Materialien des jeweiligen Messobjekts sind ebenso eine wichtige Voraussetzung für eine korrekte Bewertung thermischer Auffälligkeiten elektrischer Anlagen.
Deshalb sollten thermografische Untersuchungen an Elektroanlagen nur von Elektrofachkräften oder elektrotechnisch unterwiesenen Personen durchgeführt werden. Zu den Qualifikationsnachweisen gehören neben einer Ausbildung als Elektrofachkraft auch Zertifizierungs-Nachweise. Elektroanlagen sollte nur Fachpersonal untersuchen, das entsprechend den Forderungen der deutschen Versicherungswirtschaft das Zertifikat „Sachverständiger für Elektrothermografie“„ (IT 2 Elektro) oder „VdS anerkannter Sachverständiger für Elektrothermografie“ gemäß VdS-Richtlinie 2859 vorweisen können.
Die Zertifizierungen beinhaltet einen fünftägigen Lehrgang mit anschließender Prüfung und kosten rund 3000 Euro. Für die IT-2-Elektro- und VdS-Zertifizierung ist eine Rezertifizierung nach vier, respektive fünf Jahren erforderlich, um die fachliche Qualifikation auf einem hohen Niveau zu halten. Elektrothermografen ohne diese Qualifikationsnachweise sollten zumindest nach DIN EN ISO 9712 Stufe 1 und als Elektrofachkraft nach DIN VDE 1000-10 qualifiziert sein.
Thermografie-Messung vorbereiten und durchführen
Bei Thermografie-Messungen und Anlagen-Inspektionen sollte man Normen, Richtlinien und Vorschriften, beispielsweise DIN 54 191, die DGUV-Vorschrift 3 [10] oder die VATh-Richtlinie Elektrothermografie sowie folgende Punkte beachten:
Zusammen mit dem Auftraggeber, respektive Anlagenbetreiber sollten zunächst organisatorische Abläufe, Prüfvorgaben und Kriterien zur Beurteilung thermischer Auffälligkeiten festgelegt und schriftlich fixiert werden.
Bei der Festlegung des Messtermins sollten beispielsweise aufgrund der unterschiedlichen Temperatureinflüsse Jahreszeiten, Produktionszyklen, Inspektionen, Instandhaltungsmaßnahmen oder Anlagenstillstände berücksichtigt werden. Letztere können gegebenenfalls gleichzeitig zur Beseitigung der festgestellten Fehler genutzt werden.
Mit der Messung sollte der Thermograf erst nach einer Sicherheitsbelehrung durch den Anlagenbetreiber und nur in seiner Begleitung erfolgen. Er öffnet Schaltschränke, entfernt Abdeckungen, schließt und bringt diese nach der Messung wieder an. Bei der IR-Messung müssen stets Sicherheitsabstände gemäß DGUV berücksichtigt werden.
Damit die Wärmeemission Strom durchflossener Leiter auf dem IR-Kameradisplay gut erkennbar ist, sollte die auf die Nennbelastung bezogene Strombelastung der Anlage bei mindestens 30 % liegen.
Thermische Auffälligkeiten sollten stets mit einem Wärmebild und einem Foto dokumentiert werden, gegebenenfalls ergänzt durch eine Strommessung. Parallel sollte ein Messprotokoll geführt werden, das alle Auffälligkeiten wie Verunreinigungen, defekte Isolierungen, nicht geöffnete Elektroschränke, nicht entfernte Abdeckungen etc. erfasst.
Untersucht werden sollten alle relevanten Anlagenteile: Anschlussbereiche, Kontakte, Klemmvorrichtungen, Stromkabel oder Kabelbündel etc. Auffälligkeiten, welche die Betriebssicherheit gefährden, müssen Verantwortlichen sofort mitgeteilt und in der schriftlichen Dokumentation (siehe unten) besonders hervorgehoben werden.
Wann und wie häufig elektrische Anlagen thermografisch untersucht werden sollten, hängt von der Anlage und unterschiedlichen Faktoren ab. Bestehende Anlagen sollten regelmäßig, in der Regel jährlich untersucht werden. Je nach Alter, Zustand, Strombelastung oder Wichtigkeit der Anlage sind auch kürzere oder längere Intervalle sinnvoll. Neue Anlagen sollten vor dem Vollbetrieb unter Last untersucht werden, um mögliche Installationsfehler zu entdecken.
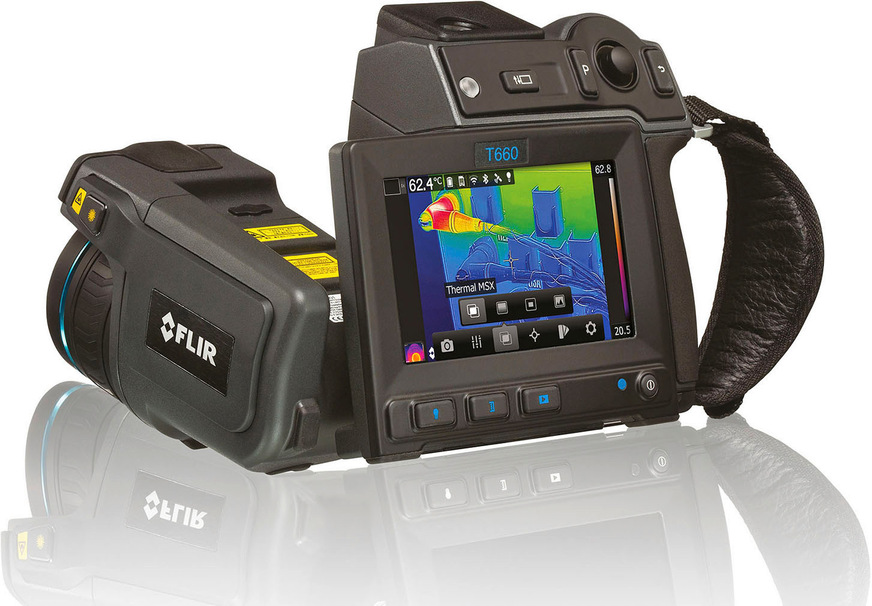
Bild: Flir Systems / Anneli Larsson
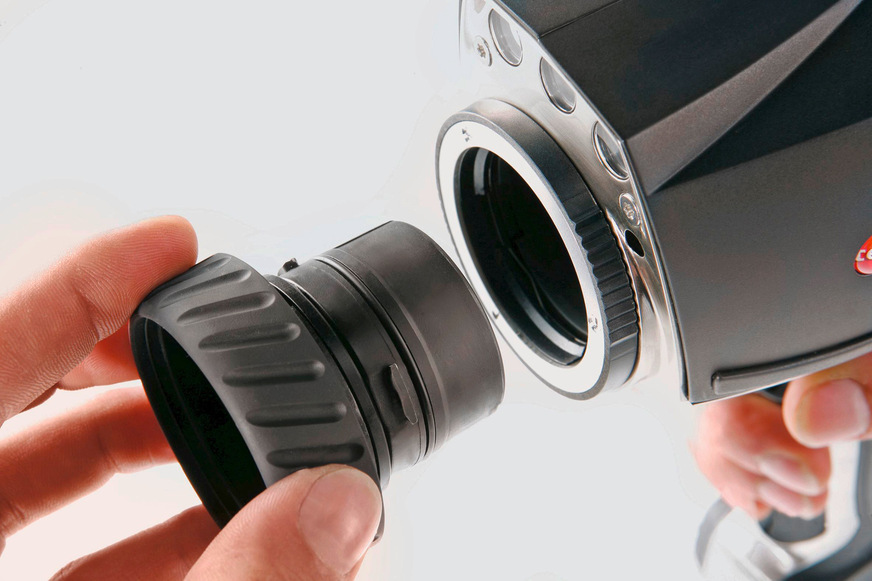
Bild: Testo
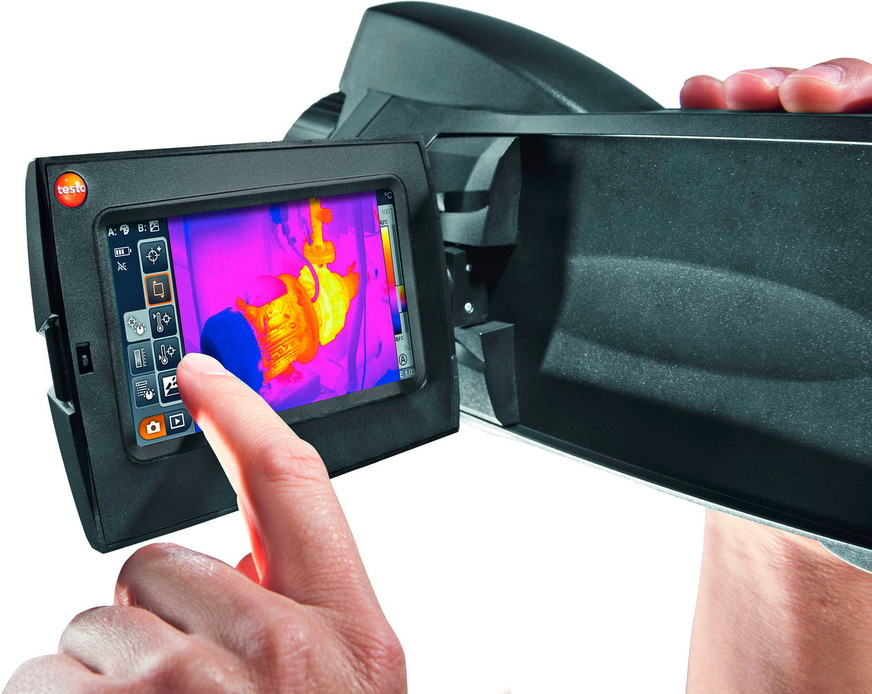
Bild: Testo
Thermografie-Berichte erstellen
Die Auswertung und Berichterstellung erfolgt in der Regel im Büro mit der zum Kamera-Lieferumfang gehörenden Auswertungssoftware. Mit ihr lassen sich Wärmebilder anzeigen, modifizieren, optimieren, organisieren, analysieren, Fotos gegenüberstellen oder mit diesen überlagern und in Verbindung mit erläuternden Texten zu Thermografie-Berichten zusammenstellen („IR-Bilder analysieren und Berichte erstellen“, TGA 10-2015).
In Thermografie-Berichten werden alle Messergebnisse dargestellt, erläutert und zusammenfassend beurteilt. Sie dienen als Entscheidungshilfe für eventuelle Maßnahmen und für eine Optimierung von Instandsetzungs- und Instandhaltungsarbeiten. Außerdem schaffen sie mehr Sicherheit, denn sie ermöglichen rechtssichere Nachweise. Deshalb sollten sie sorgfältig erstellt und zeitnah dem Auftraggeber in gedruckter Form oder als PDF-Datei übergeben werden.
Thermografie-Berichte sollten auch für Laien verständlich, nachvollziehbar und vollständig sein sowie alle relevanten Angaben gemäß VdS 2860 [8] und VATh-Richtlinie Elektrothermografie enthalten. Dazu gehören Basisdaten wie
· Auftraggeber/Auftragnehmer,
· untersuchte Objekte,
· Zielsetzung,
· Name des Thermografen und beteiligter Personen,
· Prüftermin
· eingesetzte Wärmebildkamera samt Optiken sowie
· eventuell ergänzend verwendete Messgeräte.
Der Auswertungsteil sollte Wärmebilder und Fotos aus möglichst identischem Aufnahmewinkel enthalten, inklusive Angaben zu Aufnahmeort, -datum und -uhrzeit sowie den Dateinamen. Wichtig sind auch eine hierarchisch strukturierte Objektbeschreibung (Gebäude, Halle, Schaltschrank, Schaltfeld, Bauteil, etc.) sowie der Belastungszustand der Anlage zum Messzeitpunkt in Ampere und / oder in Prozent zur Maximalbelastung.
Zu den weiteren Angaben gehören die Temperaturen der Fehlerstelle und / oder Temperaturdifferenzen zwischen Fehlerstellen und baugleichen, thermisch unauffälligen Bauteilen mit identischer Belastung sowie eine Fehlerklassifikation thermischer und nichtthermischer Auffälligkeiten gemäß DIN 54 191. Da diese Norm keine Temperaturkriterien enthält, ist es sinnvoll, für die Auswertung zusätzlich individuelle Vereinbarungen mit dem Auftraggeber zu treffen oder VdS-Kriterien zu berücksichtigen.
Bewerten und interpretieren von Wärmebildern: Herausforderungen in der Praxis
Bei der Bewertung und Interpretation der Wärmebilder sind elektrotechnisches Fachwissen und Erfahrung ebenso wichtig, wie beispielsweise das Wissen über unterschiedliche Betriebsbedingungen oder die Alterung von Bauteilen und Verbindungen.
Auffällige Temperaturwerte müssen nicht prinzipiell ein Problem darstellen, umgekehrt können auch kleine Temperaturdifferenzen auf gravierende Mängel hindeuten. In der Praxis kommt es vor allem aufgrund mangelnder Erfahrung deshalb immer wieder zu Fehlmessungen und Fehlinterpretationen, beispielsweise weil thermische Auffälligkeiten nicht hinterfragt werden oder weil Temperaturen auf Materialien, z. B. blanken Metallen, ohne entsprechende Vorbereitung gemessen werden. Das führt zu Messfehlern, weil die Wärmeabstrahlung umliegender Objekte auf der Metalloberfläche reflektiert und die Objekttemperatur dadurch überlagert wird.
Problematisch sind auch Staubablagerungen, die auf blanken Bauteilen zu einem höheren Emissionsgrad mit höherer Wärmeabstrahlung führen. Auch Sicherheitsabdeckungen aus Glas oder durchsichtigen Kunststoffen verhindern korrekte IR-Messungen. Sie sind für die Wärmebildkamera undurchsichtig, sodass nur die Oberflächentemperatur der Abdeckung gemessen wird.
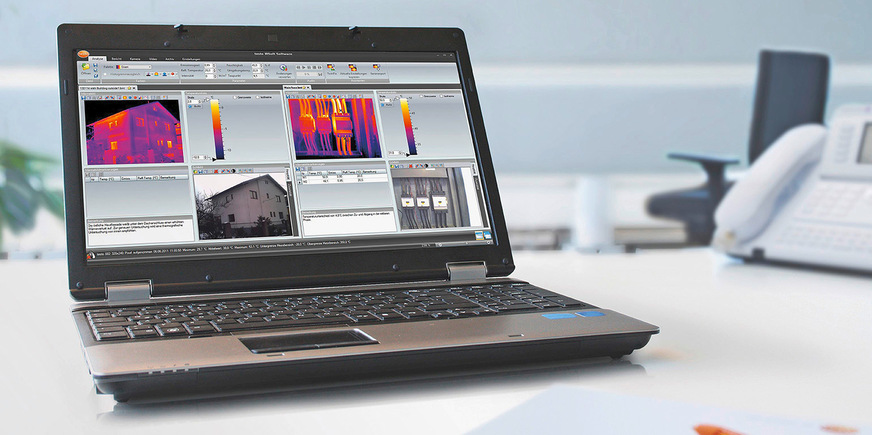
Bild: Testo
Sind ferner Funktionsweisen, mögliche Belastungen, Betriebstemperaturen, Einbausituationen oder thermische Charakteristiken oder mögliche Störungen einer Anlage nicht bekannt und werden diese nicht adäquat berücksichtigt, kann das ebenfalls zu Fehlmessungen und Fehlinterpretationen führen.
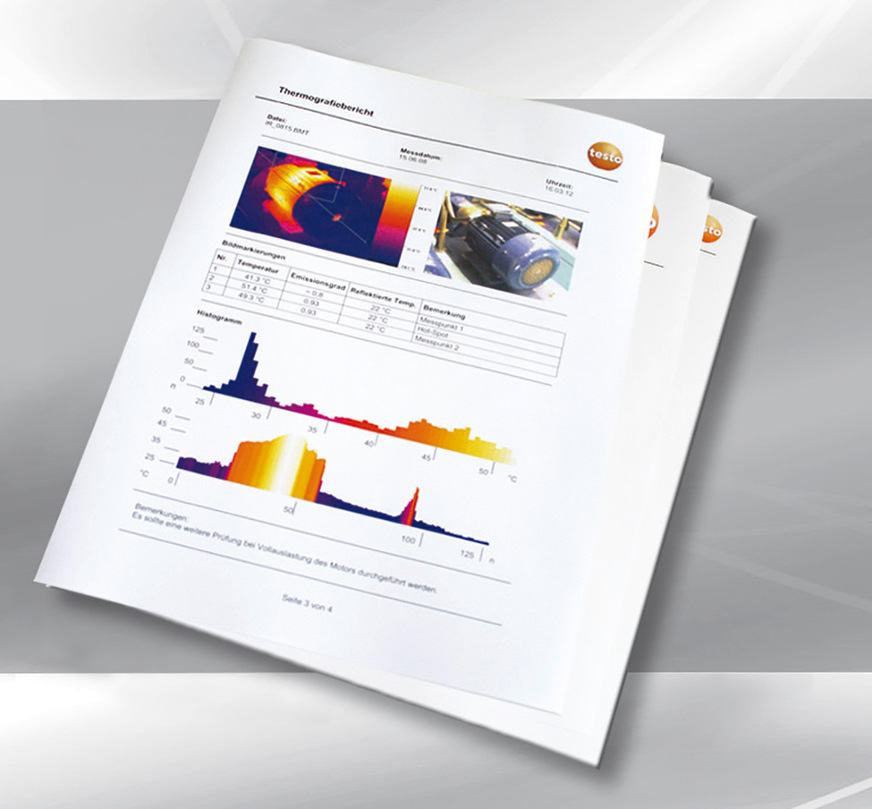
Bild: Testo
Thermografie: Ein ergänzendes Kontrollwerkzeug
Die Thermografie hat sich in der Elektrobranche als zeitsparende und wirtschaftliche Messmethode etabliert und bewährt. Allerdings sollte man berücksichtigen, dass sicherheitsrelevante Probleme womöglich erst bei hohen Belastungen auftreten. Läuft eine Anlage deutlich unter Volllast, werden Gefahren beim Thermografieren unter Umständen nicht erkannt.
Außerdem sind Mängel und potenzielle Gefahren mit einer einzigen thermografischen Untersuchung nicht immer sofort erkennbar. Beispielsweise können Erwärmungen erst bei einer höheren Anlagenauslastung oder Kriechströme erst bei starker Verschmutzung gefährlich werden.
Thermografie-Untersuchungen können deshalb kein Ersatz für wiederkehrende Sichtkontrollen, Funktionsprüfungen oder Strommessungen sein, sondern nur eine Ergänzung. Wärmebilder sind immer nur eine Momentaufnahme – deshalb sind wiederholte thermografische Überprüfungen notwendig.
Literatur
[1] DIN 54 191 Zerstörungsfreie Prüfung – Thermografische Prüfung von elektrischen Anlagen. Berlin: Beuth Verlag, Otober 2017
[2] DIN EN ISO 9712 Zerstörungsfreie Prüfung – Qualifizierung und Zertifizierung von Personal für die zerstörungsfreie Prüfung. Berlin: Beuth Verlag, Dezember 2012
[3] DIN VDE 0105-100 Betrieb von elektrischen Anlagen – Teil 100: Allgemeine Festlegungen. Berlin: Beuth Verlag, Oktober 2015
[4] VdS 2228 Richtlinien zur Anerkennung von Sachverständigen zum Prüfen elektrischer Anlagen. Köln: VdS Schadenverhütung, Februar 2018
[5] VdS 2851 Berührungslose Temperaturmessung (Thermografie) Hinweise für die Praxis. Köln: VdS Schadenverhütung, März 2011
[6] VdS 2858 Thermografie in elektrischen Anlagen, ein Beitrag zur Schadenverhütung und Betriebssicherheit. Köln: VdS Schadenverhütung, November 2017
[7] VdS 2859 VdS-Anerkennung von Sachverständigen für Elektrothermografie (Elektrothermografen); Verfahrensrichtlinien. Köln: VdS Schadenverhütung, Mai 2019
[8] VdS 2871 Prüfrichtlinien nach Klausel SK 3602, Hinweise für den anerkannten Elektrosachverständigen. Köln: VdS Schadenverhütung, März 2020
[9] SK 3602 (Feuerschutzklausel) Klauseln für die Feuerversicherung, SK 3602 Elektrische Anlagen. Berlin: Gesamtverband der Deutschen Versicherungswirtschaft, 2011
[10] DGUV Vorschrift 3 (BGV A 3) Elektrische Anlagen und Betriebsmittel, Unfallverhütungsvorschrift. Berlin: Deutsche Gesetzliche Unfallversicherung, 1997
[11] VATh-Richtlinie Elektrothermografie: Niederspannung. Elektrothermografie zur Planung, Durchführung und Dokumentation infrarot-thermografischer Messungen an elektrischen Anlagen und Bauteilen ≤ 1 kV AC bzw. 1,5 kV DC. Nürnberg: Bundesverband für Angewandte Thermografie, September 2018
[12] VATh-Richtlinie Elektrothermografie: Hochspannung. Elektrothermografie zur Planung, Durchführung und Dokumentation infrarot-thermografischer Messungen an elektrischen Anlagen und Bauteilen in Hochspannungsanlagen > 1 kV. Nürnberg: Bundesverband für Angewandte Thermografie, Februar 2016
[13] Krüll, S: Hochspannungsanlagen durch Infrarot-Thermografie optimal untersuchen, Nürnberg: VATh, Nürnberg
[14] Krüll, S: Nieder- und Mittelspannungsanlagen durch Infrarot-Thermografie richtig untersuchen. Nürnberg: VATh, Nürnberg
[15] Krüll, S: Hochspannungsanlagen durch Infrarot-Thermografie optimal untersuchen. Nürnberg: VATh, Nürnberg
[16] Marx, H.: Thermografische Inspektion von Elektroschaltanlagen – Sicherheit durch Erfahrung. Andernach: Eigenverlag, 2007
[17] Schmolke, H.: Nutzen und Grenzen der Thermografie. Berlin: Huss Medien, Elektropraktiker 59 (2005)
[18] Testo (Hrsg.): Praxisratgeber Elektrothermografie. Lenzkirch: Testo, Eigenverlag, 2017, Download
[19] Testo (Hrsg.): Praxisratgeber Thermografie für Photovoltaik-Anlagen. Lenzkirch: Testo, Eigenverlag, 2014, Download
[20] Zahorzki, F: Elektrothermografie – objektive Fehlererkennung für jedermann?. Köln: VdS-Verlag, S+S-Report 4-2006
[21] Zahorzki, F: Zustandsdiagnose als Anleitung zum Handeln. Thermografie als Werkzeug zur Umsetzung moderner Instandhaltungsstrategien. Landsberg: Verlag Moderne Industrie, Instandhaltung 7-2006
Dieser Artikel erschien zuerst in der Heftausgabe 09-2020 des TGA Fachplaners unter dem Titel „Gefahren erkennen, Anlagenwerte sichern
„von Marian Behaneck.
Weitere Infos im Web
www.thech.ch Thermografie Verband Schweiz
www.thermografie.co.at
Österr. Gesellschaft für Thermografie
www.vath.de
Bundesverband für angewandte Thermografie
www.vds.de
VdS Schadenverhütung
Lesen Sie auch:
Heizlast-Software nach neuer DIN EN 12 831
Im BIM-Projektraum einfacher verteilt zusammenarbeiten